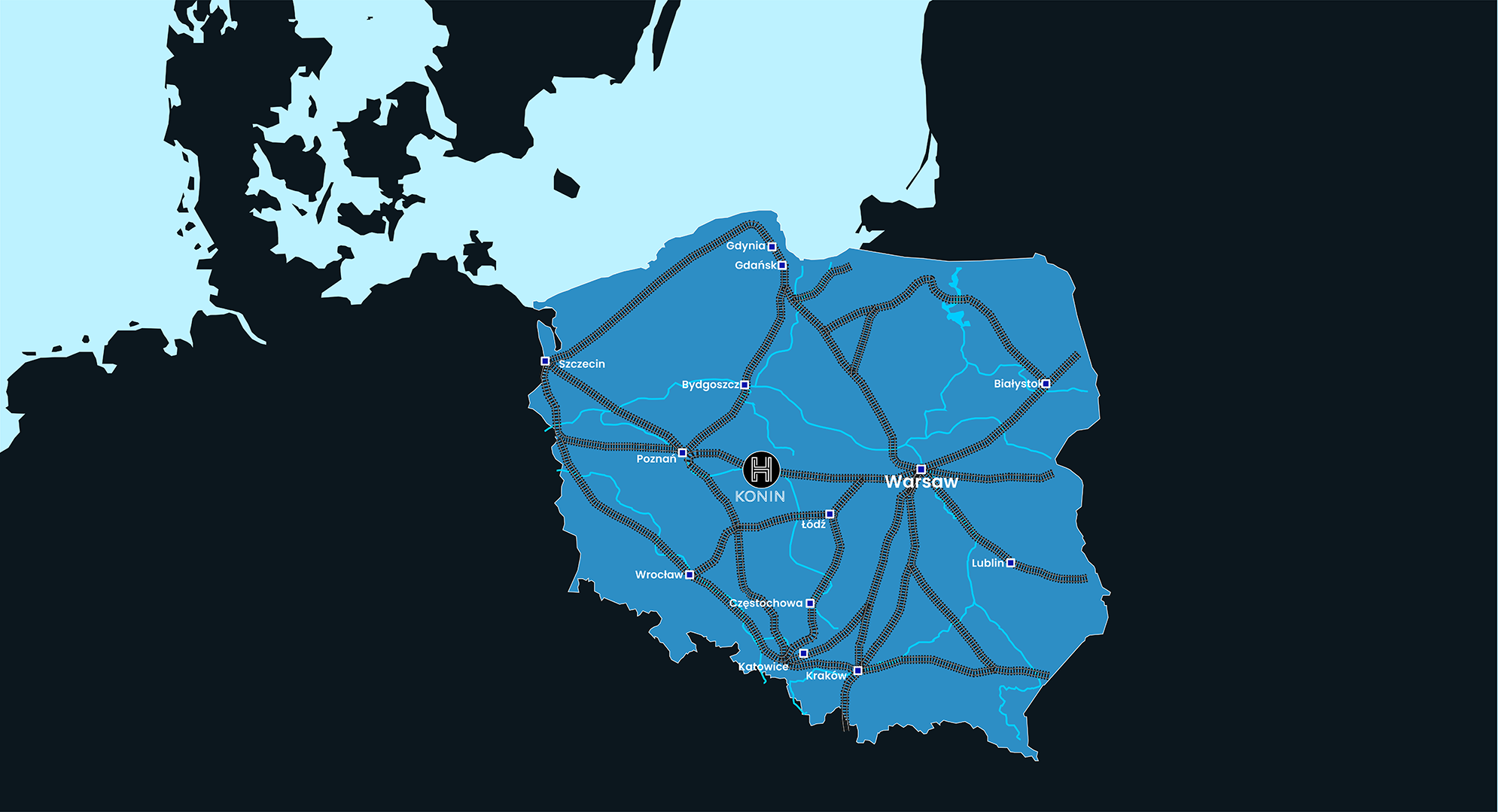
EU Konin Project
Hydrogen Utopia International will make Konin the hydrogen centre of Poland, turning 1 million tonnes of unrecyclable plastic to find its end of life; transferred into energy in Konin.
The first project by Hydrogen Utopia International is in Konin, Poland with the focus on tackling Greater Poland’s un-recyclable plastic and energy problem. We have applied for a grant of 12.5 million Euros under the EU Innovation Grant to develop a Powerhouse (AIM:PHE) DMG plant to turn plastic into hydrogen and electricity. Depending on the success of the EU funding application process, the remaining funding will be provided in the form of equity from Hydrogen Utopia International with the assistance of the London Stock Exchange licensed broker firm Turner Pope. This will be led by advisor Howard White who is a seasoned entrepreneur and investor and has an extensive experience in fund raising and the hydrogen market.
Greater Poland is one of four regions which will be sharing 8 billion Euros in the coming months to reduce CO2 emissions. As one of the biggest polluters in the EU due to its reliance on coal power stations, Poland is in need of a solution to bring its emissions in line with other EU countries with the aim to be net zero in the near future. Despite moving away from coal production since the 1990s, there is a strong dependence on the coal mining sector in the local economy, with almost half of the number of coal miners in the EU represented by 78,000 direct jobs. Konin has been identified as the region with the biggest reliance on coal and is expected to suffer substantial job losses as Poland reduces its reliance on coal fuel. Therefore the implementation of a sustainable power source in the area is very much needed.
The project in Konin will generate revenues from:
- Waste collection (gate fees)
- Heat sales
- Electricity sales
- Hydrogen sales
The project will firstly focus on supplying hydrogen to buses or other captive fleets, which won’t require heavy investments in a hydrogen distribution network. Considering that a single bus or truck uses around 12 tonnes of hydrogen per year, and that the Powerhouse (AIM:PHE) DMG Waste-to-Energy installation will have an annual capacity of hydrogen production of up to 667 tonnes, this is the first step to bringing hydrogen power to Poland in a meaningful way. As a consequence, Hydropolis United, on behalf of Hydrogen Utopia International has engaged in talks, with a number of public transport companies & waste collection companies, that could be interested in replacing their ICE vehicles with FCEV’s.
So far we have managed to sign two letters of intent with:
- Konin’s waste collection company (PGKiM Konin), which has declared a plan to acquire 10 hydrogen fuelled garbage trucks
- MPK Poznań, a public transport company, which owns and operates a fleet of 333 city buses in the City of Poznań, and intends to invest in FCEV buses
The letters of intent secured so far are still some way off securing a complete offtake of our hydrogen production capacity.
Hydrogen Fuel is the best solution for Transportation.
The new Clean Vehicles Directive requires all public procurement for new vehicles to include a certain proportion of zero-emission vehicles, which is certain to generate demand for FCE Buses
The Polish Hydrogen Strategy, set to be announced by the end of 2020 is expected to focus heavily on hydrogen use in heavy duty transport with regulatory incentives set to follow.
The National Fund for Environmental Protection and Water Management has announced that at the beginning of 2021 it will open a call for projects for zero-emission buses (both BEV and FCEV) with a total budget of PLN 1,3 billion (EUR 300 Million), with the aim of supporting the purchase of at least 500 vehicles with a funding rate of 90%.
One of the factors that currently block the development of the market for hydrogen as a transport fuel, is the insufficient supply of hydrogen with a purity level that enables it’s use in fuel cells. Poland’s annual hydrogen production is around 8.8 billion Nm3. However, this hydrogen is mainly produced by refineries and chemical plants for refining processes and fertilizer production. Natural gas steam reforming is the universally applied production method. The hydrogen that is produced by this method has a purity level of 99.95%.
To allow its use as a fuel, it is necessary to further increase its purity to comply with the standards SAE J-2719 and ISO14687-2 standards (at least 99.97%). However, due to the secondary pollution that can appear in the processes of hydrogen transportation, reloading, compression and storage, it is essential that the hydrogen that is supplied to fuel stations has better purity than the minimum requirements outlined by standards. According to the standard, the analysed hydrogen should be collected from the fuelling connection. Minor amounts of pollution can also be found in hydrogen due to contact between the fuelling connection and air, humidity or dust. This is why it’s best that hydrogen for fuelling stations is delivered in the 5.0 grade (99.999% purity).
Currently, according to our researchers in Poland only one firm (Azoty Puławy) in the south of Poland, is able to produce hydrogen of sufficient purity but it is not their standard process, and is conducted very rarely under special production regimes with very high costs- this means that pure hydrogen is not commercially available in big quantities. Almost all such hydrogen is imported from abroad – mainly from Leuna, Germany. Due to the low density of hydrogen, even at 200 bars, a single typical tube trailer is able to carry about 400 kg of hydrogen - which is two orders of magnitude less weight than is the case with conventional fuels, making hydrogen transportation very expensive. Even taking into account the new installations planned by Grupa LOTOS and Orlen SA, after completion, the Project will be the only large scale high purity hydrogen supply point for western Poland.
As a result its highly likely that the Project will be able to secure customers from most of western Poland, and not only the area closest to Konin
The plant will operate for an estimated 8000 hours per year with downtime for scheduled & unplanned outage. The plant is designed to be able to operate in three operational modes:
Power only - all of the syngas produced is routed to the gas engines (excluding that used in the Thermal Conversion Chamber burners). Depending on the plastic feedstock mix this mode will produce up to 3,4 MW net export.
1 tonne per day hydrogen production and co-production of power: 1 tpd of hydrogen will be produced with excess syngas combined with the tail gas from the hydrogen separation process being used for the gas engines. In this mode, the gas engines will be capable of producing sufficient power for the site with excess power production exported to the DNO.
Maximum hydrogen and power - all syngas is routed to the hydrogen separation system (excluding syngas used for the Thermal Conversion Chamber burners and steam boiler). This results in a maximum hydrogen production of 2,0 tpd, depending on plastic feedstock and the operating conditions. In this case the gas engines will operate on hydrogen separation system tail gas and the net output power will be exported.